
Monnalisa

Automatic polishing system with fixed bench composed of:
– PGM: automatic motorized rotating platform for handling workpieces
– Robot: robotic loading and unloading system with slab warehouse, able to work without operator, entirely connected to the company network.
– a Hercules carriage equipped with 5 planetary heads for polishing straight edges
– an Athena carriage equipped with profiling/shaping spindle and automatic 12-position tool changer
GENERAL EQUIPMENT OF THE MACHINE
- Electrically controlled reference squares for the workpiece alignment (workpiece projection from the bench: 150 mm).
- Spindle holding carriage, moved by a toothed belt controlled by electric system (brushless motor). Speed 0÷100 m./min.
- Spindle positioning axes assembled on ball screw guides controlled by digital motors.
- Centralized lubrication sistem controlled by electric pump.

- Machine with a fixed bench and a travelling holding spindle carriage;
- Electrowelded loading bench with the guides for the carriage traverse placed on the back of the bench;

Set of 8 pneumatic slab holding pistons

Ultrasonic sensor for slab length and position

CNC-control unit with 19” touch screen control panel

8 lines of multidirectional rollers in the bench, with pneumatically controlled up and down movement
“ATHENA” CARRIAGE
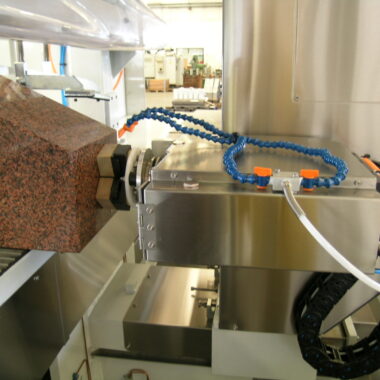
Spindle holding carriage, moved by a toothed belt controlled by electric system (brushless motor).
Speed 0÷100 m./min.
Spindle positioning axes assembled on ball screw guides controlled by digital motors.
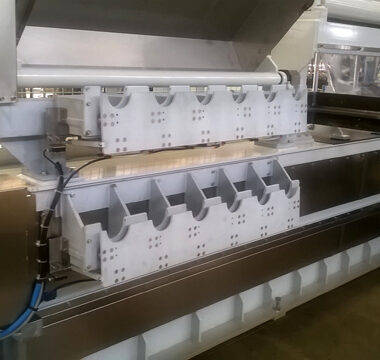
12-position automatic tool change
With the function “twin tools” it’s possible to load the same type of tool in two or more positions in order to avoid that the machine stops when a tool is worn out, thus increasing the autonomy of the machine.

Possible processings:
- Polishing of straight edges
- Shaping and polishing of shaped edges
- Partial polishing
- Possibility to polish straight edges of different thicknesses at the same time;
- Possibility of drawing irregular profiles directly on the touch screen panel
OTHER WORKINGS
- Shaping and polishing of conic bevels
- Slanted edges
- Partial shaping
- Shaping of narrow workpieces (work table overhang 50 mm)
- Shaping of multiple edges with different profiles and thickness, until a maximum of 5 work pieces with manual loading
- Possibility of shaping special profiles on straight edges with shaping tools (max. thickness 40 mm – max. thickness of the shaping tool 130 mm).
“HERCULES” CARRIAGE

Carriage with 5 spindles “TP” with 4 satellite spindles for polishing straight edges, max thickness 350 mm.
Carriage movement on ball recirculation guides motorized by brushless motor.
Speed: 0 – 30 meters / minute
The 5 satellite spindles are mounted on a vertical recirculating ball guide driven by a brushless motor for automatic centering of the heads on the thickness of the work piece.
Electronic equipment that allows the use of spindles in different ways:
– in passes for each single spindle (with possible vertical or horizontal oscillation of the polishing heads)
– single pass with automatic intervention of all the spindles simultaneously
PGM: MOTORIZED ROTATING LOADING PLATFORM

Motorized rotating platform to operate independently on all 4 sides of the plate.
The platform is connected to the CNC of the machine, from which it receives information on the number of sides to be processed and, based on these data, automatically moves, positions and aligns the slab into the work area. After a side is finished, the platform rotates the workpiece and repositions it to execute the work cycle on the next side.
Main characteristics
- Refrigerating system with automatic opening, closing and flow control device
- Automatic machine stop device in case of lack of air
- Automatic machine stop device in case of worn out tools
- Perimeter fence for operator safety
- Software package with preset templates, with possibility to modify both the geometric parameters of the profiles (for example the size of the chamfers), series of tools to be used and their working parameters
- Possibility to program and work until 5 pieces of different thickness and profile at the same time
- Mobile panel for manual movements of the platform and clamping pistons
- Manual solenoid valve for excluding the pistons
- Water draining system
- Automatic centralized lubrication
- Solenoid valve for the water supply on each single spindle
- Stainless steel covers
- To prevent rusting of machine, the structure and the main components are metallized using a modern treatment composed of several phases: sandblasting, metallizing with zinc wires, epoxy paint with zinc phosphate, and final paint coat with polyacrylic polish. The covers are in durable stainless steel. All other metal sheets on the machine have been treated by cataphoresis in sequence they have gone through a degreasing bath, a pre-treatment full immersion, an electroplated bath that uses power to lay paint creating a uniform and consistent film after the rinsing is complete, it is then all baked and sealed in an oven.
- Monolithic machine (made in one piece – excluding the rollers) that does not need foundations but can lay on the floor
- Machine prepared for remote assistance by cable (to be supplied by the customer)
TECHNICAL DATA
ROBOT GANTRY

Robot with 3 controlled axes (X, Y and Z)
Axis X stroke about 6500 mm speed 40 mt / min
Y-axis stroke about 1800 mm speed 40 mt / min
Z axis travel up to about 2700 mm speed 15 m / min

Lifting system with two coated forks for handling slabs
Support columns for the electro-welded framework with
Perimeter protection system.
Geared motor transmission with rack and pinion system

N ° 2 cantilever-type fixed warehouses with 19 positions for loading and unloading of raw and polished slabs
The two warehouses can load up to a maximum of 19 pieces, of which 7 with a thickness of 15 cm and the others with a thickness of 10 cm.
Maximum height of the whole system 6 mt.
Possibility to adapt the warehouse to customer needs.

Loading and unloading bench equipped with sensors for automatic slab measurement.

Touch screen control panel
PROJECT DATA:
Working method:
The operator places the rough slabs on the loading / unloading table and inserts the slab data into the job list.
The robot automatically moves the piece from the loading table on the rack, measuring the size of the slab.
Upon request of the Comandulli machine, the robot will move a piece from the rack to the workstation on the PGM rotating platform. At the end of processing the PGM will move the piece back to the position in which the robot can pick it up to reposition it in the rack.
The operator will then discharge the finished work pieces by sending appropriate commands to the robot that will take them from the rack and place them on the loading / unloading table.
The operations of the loading / unloading bench controlled by an operator can be carried out while the system is busy working the pieces inserted in the job list. This allows the system to be engaged in a potentially infinite work cycle.